Warmia and Masuria are in full swing, saying goodbye to coal and welcoming green fuels, and reducing emissions and landfill gasses.
By Konrad Nowak, Chairman of the Managing Board of MPEC Sp. z o.o.
Nicholas Copernicus and his Green Haven
Olsztyn is the largest city in north-eastern Poland, dubbed the Land of Thousand Lakes. The city is home to 170 thousand people, with 1.4 million in the region. The city is over 650 years old and picturesquely located among woods and lakes. Olsztyn has several forests within its borders, including one of the largest city parks in Europe – the City Woods.
The city was also where Nicholas Copernicus resided and wrote his theses, and today, as the capital of Warmia and Masuria, it is a dynamically expanding agglomeration. Michelin, the world tire industry leader, has its production facilities here, and the tire industry is one of the key sectors the region’s development strategy is focused on, together with the lumber and furniture industry and high-quality food.
A long, long time ago
The company dates back to the 1970s, although district heating in Olsztyn started as early as 1888-1890 when the city gas plant was equipped with steam and gas boilers. Coke was used to heat the first buildings, and heat was delivered via brick canals. Then, the number of local boiler rooms mushroomed until the Second World War, when many were destroyed.
When the remaining ones were counted after the war, there were 240 of them, 80% were non-functional. In the early 1960s’ in Olsztyn, there were 400 of them, and when the city was selected as the location for a new tire factory (the Michelin factory now), a large heat plant was built, supplying its heat surplus to nearby housing estates.
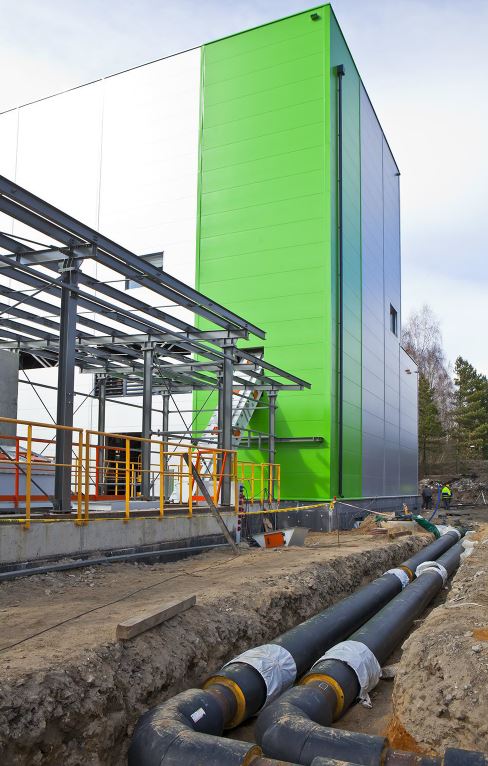
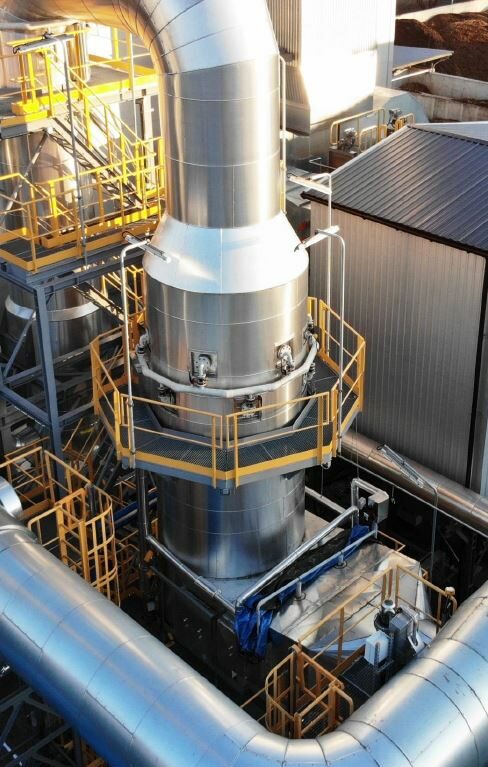
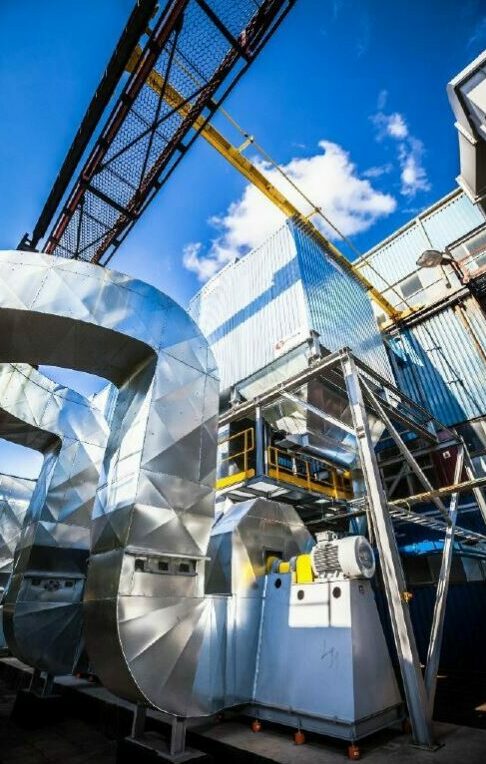
A new heat plant has been built.
The 1970s and 1980s were a period of rapid DH network expansion. Olsztyn was growing fast, and it was decided to replace 200 local boiler rooms with a centralised heat source. In 1975, the construction of the city heat plant started. Four years later, it was the second main source of heat (apart from the tire factory heat plant) for the residents of Olsztyn while heat transfer pipes were laid.
1988 Miejskie Przedsiębiorstwo Energetyki Cieplnej (MPEC) – the city DH enterprise- was created. One of its principal tasks was a takeover of local boiler rooms from the military and health and education services to cover the city with a uniform DH network. At that stage, it was apparent that the heat efficiency needed to be increased, losses in transfer decreased, and the best solutions applied.
In the middle of 1990, MPEC Olsztyn was the first company in Poland to use modern, Danish-made pre-insulated pipes in its network. In the early 1990s,’ MPEC Olsztyn covered a major share of Olsztyn’s needs regarding district heating and hot domestic water.
In 1991, another significant change took place – MPEC Olsztyn’s owner was now the city of Olsztyn, which took over the company’s ownership from the State Treasury. In 1997, it became a municipal company, with the city holding 100% of its shares.
Comfort and attractiveness of the district heating
Today, MPEC generates energy from its two sources – the city heat plant Kortowo, which has five hard coal-fired boilers with a nominal capacity of 29 MW, and Kortowo BIO, equipped with a 25MW-boiler with a 4MW flue gas heat recuperator, using wood chips as the source of fuel.
An external source of heat is the CHP plant of the Michelin plant, where MPEC Olsztyn contracts 100 MW of thermal power. MPEC also has local gas-fired boiler rooms with a total capacity of approx. 5 MW and two gas engines with a total thermal capacity of approx. 1.3 MW.
MPEC has been constantly investing in its heat sources and expanding and competing, bearing its customers’ benefits in mind. It has been replacing its old, worn-out channel-type DH network with a modern, pre-insulated one.
Out of 170 km of network, 122 km are now the modern pre-insulated type, characterized by much lower transfer losses, increased efficiency, and better environmental properties. It interconnects 1 573 substations. There are four pumping stations within the network, improving heat distribution considerably. Constant development and modernization of the network allow for connecting new consumers.
Currently, over 60% of Olsztyn inhabitants and institutions use district heating. What is the secret? Quality of service comes to mind first. Safety of deliveries, comfort, and reliability are combined with the customers’ opinion that DH heat is environmentally friendly. A significant benefit of the city-delivered heat is its socially accepted price level.
CAPEX
Last year, MPEC Olsztyn invested over EUR 10.5m, increasing the CAPEX level to EUR 15.7m in 2020. The network expansion and the creation of over a hundred new substations will allow new customers to connect. MPEC has also been replacing group substations with individual ones to reduce costs.
There is a growing interest in connecting to the DH network, with new connections planned as far ahead as 2022. An important task will be connecting to the network of one of the largest housing co-operatives in Olsztyn, which, up to now, has been supplied directly from the Michelin heat plant. Michelin will soon stop delivering the heat to the city, however.
MPEC-generated heat now becomes the choice of housing co-operatives and developers building new buildings and more and more small housing communities, including those from the older parts of town. People appreciate the reliability and functionality of this solution in comparison to the need to have their own gas-fired boiler. The Olsztyn DH network has also been supplying buildings outside the city limits – one of the neighboring municipalities chose the safe and comfortable MPEC heat.
A new era of district heating – new challenges
Today’s MPEC faces new challenges related to system functioning efficiency and ecological demands. A few years ago, preparations started transforming the heat generation model, which used to be 98% coal-based. The first step was erecting a 25 MW modern, automated biomass-fuelled heat plant in 2019. The biomass used as fuel there is in the form of post-timber production wood chips, characterised by high humidity.
An important component of the heating plant is the flue gas heat recuperation system, upgrading the total efficiency of the plant to 93%. Also, coal-fired boilers in the city heat plant are undergoing modernization by installing a modern flue gas cleaning system. Reducing dust, SO2, and NOx content will allow the source to meet the BAT requirements while decreasing total emissions four times and increasing heat generation efficiency.
Investment to change the Olsztyn power and waste management sector
Another new project is a municipal waste thermal treatment plant. In the incinerator, the waste product (after recycling) will be used as a heat source and then supplied to consumers. The plant will be a highly efficient cogeneration facility, also producing electricity.
Waste collection for the plant will cover 700 thousand inhabitants of the region, treating <30% of the waste unsuitable for recycling and reuse. It is worth noting that the domestic institutions and the European Commission appreciated the project of using the waste as a fuel source, which granted EUR 40m for the project.
The installation will meet the most stringent environmental criteria, exceeding even the current norms required by the new BAT Conclusions. The plant will be a state-of-the-art installation both in Poland and in Europe. The system will be supplemented by an independent gas/oil boiler system of 70 MW capacity.
The entire installation is within the public-private partnership framework, thanks to which the voivodship will acquire a modern installation for waste thermal processing and Olsztyn, an ecological source of heat to cover the needs of its inhabitants for many years to come. The plant is scheduled for launch in mid-2023.
Energy Efficient System – the only constant is constant change
The company hopes to achieve the status of an energy-efficient DH system over the next few years. Hence, investments in an environmentally friendly energy system and increasing energy efficiency are required to meet the new standards and avoid harsh penalties connected with rising CO2 emission costs.
This will, in turn, translate to stabilizing heat generation and waste management costs. Already, a reduction of 60k tonnes of CO2 is assumed per year. After the construction of the new CHP, it will further increase by 75k tonnes. The emission of landfill gases will decrease by almost a million tonnes.
After the investment is completed, the energy sector profile in Olsztyn will look very different. In the modernized system, the heat will be generated 57% from locally sourced renewable fuels (municipal waste and biomass) and only 39% from coal. Natural gas will supplement the remaining 5%. MPEC faces a series of further challenges, like achieving coal independence, as 2050 it will be eliminated from the fuel mix.
For further information, please contact Konrad Nowak, knowak@mpec.olsztyn.plat